An extraordinary study of epoch-making importance: the first to scientifically validate the accuracy of margin closures and occlusion of whole crowns fabricated withDGSHAPE DWX-52D Plus
Henriette Lerner, Katalin Nagy, Nicola Pranno, Fernando Zarone, Oleg Admakin, Francesco Mangano.
Trueness and precision of 3D-printed versus milled monolithic zirconia crowns: An in vitro study.
Journal of Dentistry, 2021, 103792, ISSN 0300-5712
Abstract: Purpose
To compare the trueness and precision of 3D-printed versus milled monolithic zirconia crowns (MZCs).
Methods
A model of a maxilla with a prepared premolar was scanned with an industrial scanner (ATOSQ®, Gom), and an MZC was designed in computer-assisted-design (CAD) software (DentalCad®, Exocad).
From that standard tessellation language (STL) file, 10 MZCs (test) were 3D-printed with a Lithography-based Ceramic Manufacturing (LCM) printer (CerafabS65®, Lithoz), and 10 MZCs (control) were milled using a 5-axis machine (DWX-52D®, DGShape).
All MZCs were sintered and scanned using the scanner above.
The surface data of each sample (overall crown, marginal area, occlusal surface) were superimposed to the original CAD file (ControlX®, Geomagic) to evaluate trueness: (90-10)/2, absolute average (ABS AVG) and root mean square (RMS) values were obtained for test and control groups (MathLab®, Mathworks) and used for analysis.
Finally, the clinical precision (marginal adaptation, interproximal contacts) of test and control MZCs was investigated on a split-cast model printed (Solflex350®, Voco) from the CAD project and compared.
Results
The milled MZCs had significantly higher trueness than the 3D-printed ones, overall [(90-10)/2 printed 37.8 µm vs. milled 21.2 µm; ABS AVG printed 27.2 µm vs. milled 15.1 µm; RMS printed 33.2 µm vs. milled 20.5 µm; p = 0.000005], at the margins [(90-10)/2 printed 25.6 µm vs. milled 12.4 µm; ABS AVG printed 17.8 µm vs. milled 9.4 µm; RMS printed 22.8 µm vs. milled 15.6 µm; p= 0.000011] and at the occlusal level [(90-10)/2 printed 50.4 µm vs. milled 21.9 µm; ABS AVG printed 29.6 µm vs. milled 14.7 µm; RMS printed 38.9 µm vs. milled 22.5 µm; p = 0.000005].
However, regarding precision, both test and control groups scored highly, with no significant difference in the quality of interproximal contact points (p = 0.355) or marginal closure (p = 0.355).
Conclusions
Milled MZCs had statistically higher trueness than 3D-printed ones; however, all crowns showed high precision, compatible with clinical use.
Clinical significance
Although milled MZCs remain more accurate than 3D-printed ones, the LCM technique seems able to guarantee the production of clinically precise zirconia crowns.
Keywords: Monolithic zirconia crowns; 3D printing; Milling; Trueness; Clinical precision
(https://www.sciencedirect.com/science/article/pii/S0300571221002153)
https://doi.org/10.1016/j.jdent.2021.103792
View and download PDF
Details of the 3D-printed and milled monolithic zirconia crowns (MZCs). In total, 20 samples were manufactured. Ten MZCs (test group, left of the picture) were 3D printed with a lithography-based ceramic manufacturing (LCM) printer (Cerafab S65®, Lithoz, Vienna, Austria). The other 10 MZCs (control group, right of the picture) were milled with a 5-axis milling machine (DWX-52D®, DGSHAPE, A Roland DG Company, Hamamatsu, Japan). All crowns were sintered following the manufacturer’s recommendation and were ready for analysis. Different colors were used to facilitate the allocation of the samples in the correct group, eliminating any risk of confusion. (For interpretation of the references to color in this figure legend, the reader is referred to the web version of this article.)
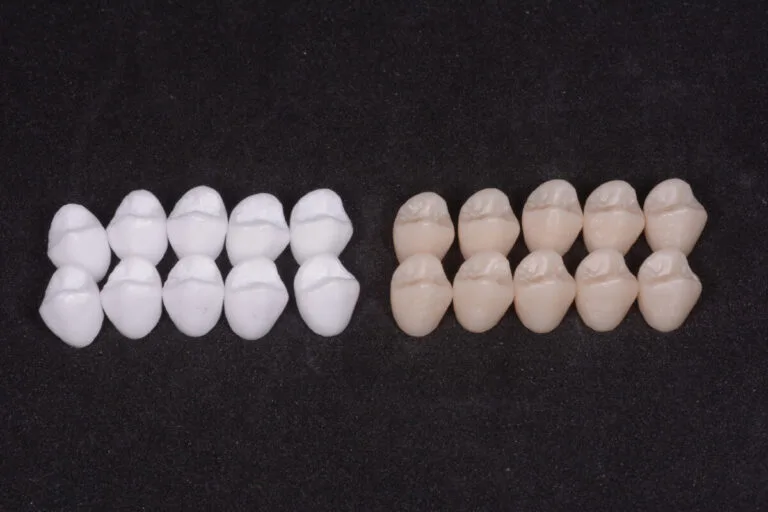
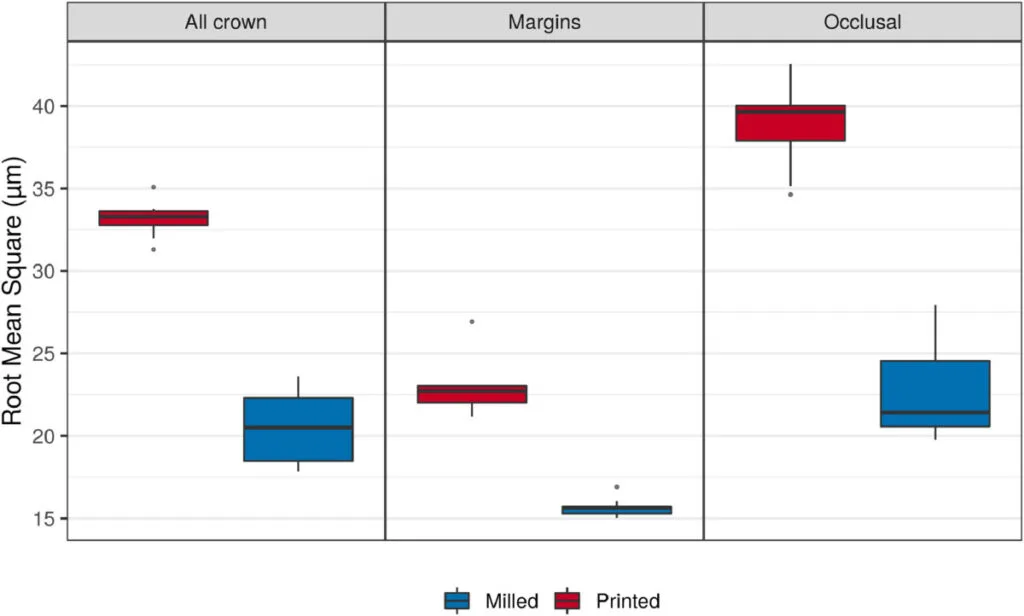
As it works toward future business expansion, DGSHAPE is promoting activities to reach the mid-term objectives of “strengthening the ability to support new dental materials,” “acceleration of global expansion,” and “developing high value-added solutions for the dental industry“ In the dental market, an essential requirement for DGSHAPE is to support new materials. Therefore, we pay close attention to the new product offerings of material manufacturers and the needs of patients and dental clinics to offer optimal processing methods as quickly as possible.