“When you’ve been in this industry long enough, you can tell right away when a product or process will change everything. Digital dentures were one of those moments for us. But with the Digital Denture workflow, it’s not just digital
it’s human, it’s personal, and it’s scalable.”
Who We Are
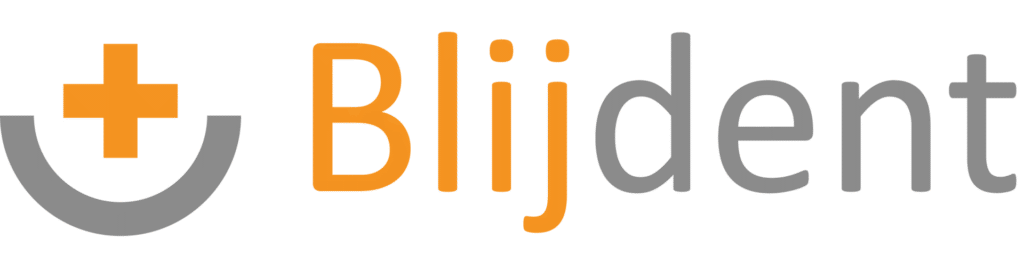
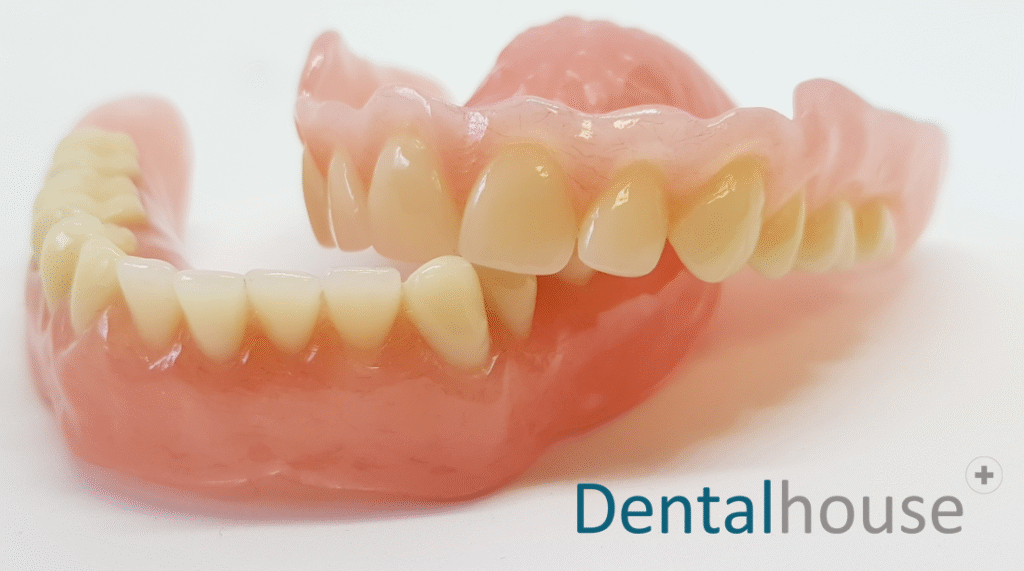
At Blijdent, we’ve always been about more than just equipment. Since 2012, we have provided innovative equipment, software, materials, and training to drive digital transformation in oral care.
As part of the broader Dentalhouse group which includes Digidenture (our in-house dental lab), Multident, our training academy, and a fully operational digital clinic, we offer more than just products. We provide a full digital workflow, along with expert training, support, and data management.
We’re based in the Netherlands, where the denture market is unique: most dentures are publicly funded, and the government caps prices with insurance covering up to 70%. So private options are limited.
Working in this controlled environment, the need for quality, efficiency, and aesthetics is more important than ever.
Why We Went Digital
We knew early on that the traditional denture process—messy wax-ups, multiple try-ins, variable fits—was becoming outdated. That’s why we began working closely with DGSHAPE milling machines and building a full digital workflow for what we now proudly call “Natural Dentures”.
Our clinic works with a certified Clinical Dental Technician (CDT), who provides patients with high-quality full dentures. We currently produce around four cases per week, with each upper and lower set averaging €1,200.
Every denture is created using conventional acrylic and teeth, but with the precision, reliability, and repeatability of digital milling.
Our dedicated training center and digital laboratory help us turn technology into real clinical outcomes—and teach others to do the same.
Why Digital Dentures with DGSHAPE Feel Truly Natural
Workflow: We utilize the DWX-53DC in conjunction with the DK2-53-TR denture kit and DGSHAPE Dental CAM v3.4.8 to produce what we refer to as “Natural Dentures”—a comprehensive digital solution designed to create dentures that closely resemble the appearance and feel of natural teeth.
DGSHAPE Digital Dentures offer:
Realistic aesthetic, thanks to full control of tooth and gingiva design
Highly personalised result, allowing the CDT to adapt each design to the patient’s facial features and wishes
Better fit, due to zero shrinkage of materials
Durability, with stronger monoblock structures
Faster workflow, where even the milled try-in can be used directly in the mouth—no wax, no melting, no guesswork.
By using a milled monoblock denture as a try-in, we save a huge amount of chair time and avoid material unpredictability. And because the fit and occlusion are highly accurate, patients experience comfort from the first fitting.
Many labs in the Netherlands still don’t fully believe in digital. But for us, it’s simple: if you can offer better results, in half the time, with fewer remakes—it’s not a gamble. It’s the new standard.

Why It Works: The Value Behind Digital Dentures
At the heart of our Digital Dentures process is a simple question: How can we deliver more value to both patients and professionals without compromise? Here’s what we’ve found.
For Patients
For Dental Techincians and Clinics
When a patient receives a Natural Denture, they experience more than just a replacement for lost teeth. They receive:
Durability – A long-lasting solution made from quality acrylic and teeth
Better Fit – Thanks to digital milling, there’s no material shrinkage and fewer adjustments
Natural Aesthetics – The denture is tailored to their facial structure, personality, and preferences
Confidence – A great fit and look means better comfort and self-esteem
As a clinic, we’ve seen patient satisfaction increase, and with fewer remakes or follow-ups, everyone benefits.
As users of the workflow, we benefit from:
Use of conventional materials – Acrylic and denture teeth are still the standard, so there’s no need for expensive new materials
Excellent fit – Precision milling means a reliable result every time
High predictability – No surprises, no shrinkage, no need to restart
Aesthetic control – Every detail can be adjusted digitally before milling
50% time saving – A massive efficiency gain without sacrificing quality
Future-proofing – The workflow evolves as technology does. Labs that adopt it now are better positioned for the future
In a market that still sees digital as a “nice to have,” this workflow proves that it’s smarter, faster, and more personal.
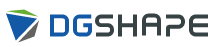
Building the Future with DGSHAPE
We’ve already invested in three DGSHAPE milling machines dedicated exclusively to denture production. Every technician we train in our academy learns the Natural Denture process—not as an add-on, but as the standard of care we believe in.
With DGSHAPE’s support, we’ve managed to cut production time by over 50%, improve consistency across cases, and future-proof our business. While the upfront cost savings are minimal, the real benefit is in predictability, workflow control, and patient satisfaction.
We also see ourselves as evangelists in a market that’s still sceptical.
As DGSHAPE Official Resellers we offer the Digital Denture KIT as a bundle with DWX milling machines.
Tooth-setting simplified
Easily fit carded, milled, or printed teeth into milled pockets
Affordable aesthetic solution
Create aesthetically pleasing, custom-made full dentures in-house and save money instantly
Faster turnaround time
Employ this digital workflow and put the time you save back into your business
Heat-cured compatible
Choose to use heat-cured or cold-cured acrylic with your denture kit
Open Solution
The denture kit is compatible with the latest CAD software, including 3Shape’s Dental System and exocad